In general, we can define the burst pressure in a drill pipe as the differential pressure acting across the drill pipe wall due to an internal pressure greater than the external pressure. In this article, we shall discuss the drill pipe burst pressure formula and calculations used in drill string design.
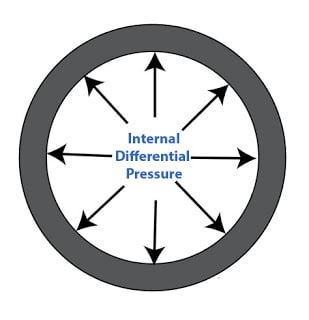
How To Consider Burst Pressure While Selecting Drill Pipes
Unlike Casing Design and tubing design, burst is seldom a controlling criterion for Drill Pipe design. This circumstance is because the load line and backup lines are controlled by the mud inside and outside of the drill pipe, respectively. In all but the most unforeseen cases, these two mud weights will be the same. Therefore, the imposed surface pressure controls the burst load line (Fig. 1).
In addition, in most unusual circumstances, such as well kick control or squeeze cementing, a backup pressure applied to the Casing resists burst. The maximum burst load normally occurs at the depth without external pressure or backup.
This normally occurs at the surface just below the wellhead, where there is often no surface pressure. To determine the maximum allowable burst load, a safety factor of 1.125 must be used.
PBurst = Internal Pressure – External Pressure
Minimum Internal Yield Pressure
The MIYP of the pipe body is determined by the internal yield pressure formula found in API Bull. 5C3, Formulas and Calculations for Casing, Tubing, Drill Pipe, and Line Pipe Properties.
- PB = Minimum internal yield pressure
- Yp = Minimum yield strength (psi)
- t = Nominal wall thickness (in)
- D =Nominal outside diameter of the pipe (in)
A pressure at MIYP does not mean the pipe will have a burst or rupture failure, which only occurs when the tangential stress exceeds the ultimate tensile strength (UTS). So using a yield strength criterion to measure pipe internal pressure resistance is inherently conservative. This is particularly true for lower-grade materials such H-40, K-55, and N-80 whose UTS/YS ratio is significantly greater than that of higher-grade materials such as P-110 and Q-125.
Final Words
In general, a Drill Pipe should not be used in applications requiring high burst-pressure loading if gas is the high-pressure source. Premium Tubing (i.e. Hydril, VAM Connections) connections are usually better suited to this service than used Rotary Shouldered drill pipe connections. In no event should a Drill Pipe of any grade be used to carry gas containing hydrogen sulfide having a partial pressure greater than 0.05 psi.
For other applications, burst pressure ratings for the Drill Pipe can be found in Table 1. These ratings have been calculated assuming minimum material properties and no axial load. A design factor of 1.176 is standard and should be divided into the Burst rating of the Drill Pipe tube to set its maximum burst pressure differential. While simultaneous tension increases the tube’s burst pressure capacity, this benefit is often ignored.