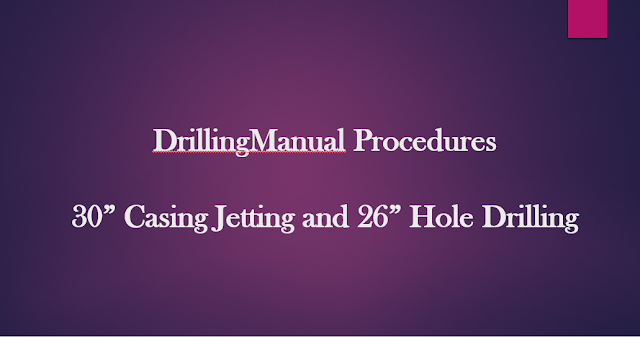
1) Establish length of 30” casing to be jetted. Paint the top 4m WHITE with 1m spacing bands (in Black) from the Casing head (or other reference point) down the GRA and onto the casing. It is also helpful to likewise paint the bottom 3-4m from the casing shoe (makes observation by the ROV much easier).
2)Take EXACT measurements of casing length from hang-off point to shoe.
3)Having established the required length of casing, it is now necessary to measure accurately the components of the Jetting BHA, including the distance from the base of the 30” CART/Drill-ahead to the latching point. REMEMBER, that under normal circumstances the CART will drop approximately 10 cm once latched into the 30” casing housing.
PHYSICALLY GAUGE I.D. OF 30” CART AND ALL DRILL COLLARS, JARS, SUBS TO BE RUN ABOVE THE CART.
4)The BHA should be designed to ensure that the base of the bit is approximately 4 – 6” OUTSIDE the 30” casing shoe. This is the optimal position for jetting. Usually it is possible to interchange drill collars and/or XO subs to achieve this spacing. If the bit is too far inside the casing then the flow pattern is too narrow and insufficient material will be jetted away to allow the casing to freely descend. If the bit is too far outside the casing, then excessive washout may occur.
IF THE AVAILABLE EQUIPMENT DOES NOT ALLOW FOR NECESSARY SPACING THEN THE CASING SHOULD BE CUT TO AN APPROPRIATE LENGTH.
5) The BHA is made up with a 26” bit, Mud Motor and MWD. This is all tested for correct operation, then racked back in the rig derrick.
6) GRA is located onto dollies in the moon-pool, beneath the rotary table.
7) 30” Casing is run and landed into the GRA.
8) BHA is made-up again and run inside the GRA and 30” casing.
9) 30” CART/Drill-ahead is made-up into the BHA. It is also possible to test the operation of the latching lugs at this time by turning the requisite number of turns to the left (3 for Vetco and FMC CART’s).
10) The whole assembly is lowered until the CART rests in the casing head and can then be latched into place (3 turns to the left). This is often easiest done with the use of a chain-tong.
THERE MUST BE NO FURTHER ROTATION OF THE STRING
11) Once correctly engaged, the position of the bit is then verified by the ROV. Roughly 1/2 of the cone depth should be visible below the casing.
12) The whole assembly is then picked-up to ensure correct latching of the CART to the GRA/casing, the dolly is removed and the string run-in hole on drill-pipe.
13) As seabed is approached the ROV is used to verify contact with seabed, the drill-pipe is marked and then strapped from the previous connection to determine Mudline depth.
14) It may be possible to run an MWD survey to verify verticality of the casing. On occasions, there is too much “noise”, due to movement of the BHA inside the casing, to be able to decode the MWD signal.
15) Running ROV is now used to check the GRA Bull-eyes and to perform the positional surveys. It may be necessary to move the rig to be in the correct position.
16) Total string weight should be noted, and, the WOB indicator set to Zero (it should not be re-adjusted further).
17) Jetting commences at low flow rate and with 0 klbs for the first few meters then 0-2 klbs usually up to the first 13-15 m. The weight should be kept AS LOW AS POSSIBLE at this first stage to ensure that the 30″ casing remains vertical. DO NOT RUSH.
18) The ROV should check around the base of the 30″ casing for cratering caused by excessively high flow-rate. Should cratering be seen then the flow-rate must be reduced accordingly. The ROV should also monitor that the cuttings returns are exiting through the CART.
19)While casing running & once the 30″ casing starts to take weight (9-13 m rouglhly) it should be picked up to help free-up hole drag. From this point on wards it is necessary to pick-up the casing every 3-6 m (sometimes more frequently) to reduce the hole drag. For. We keep the WOB to 80 % of the supported casing string weight at a given depth…to avoid buckling the casing). If this is not done frequently then things quite quickly get quite tight!! The casing should usually be picked up 3-5 m above the interval that has just been jetted, this makes a significant difference in reducing hole drag from just picking up over the 3-6 m that have just been jetted. The deeper you get the longer the interval you should pick up over.
IT HAS BEEN OBSERVED THAT “REAMING” THE CASING 2-3 TIMES EACH TIME ALSO SIGNIFICANTLY REDUCES THE DRAG.
20) Flow rate and WOB are gradually increased while running 30″ casing. When only 2-3 m are left to jet in, reduce the flow rate to the minimum for the motor to operate.
21) 40 bbl sweeps of Bentonite mud (or Hi-vis mud) should be circulated out every ½ stand and prior to every connection. The Bentonite is normally significantly more effective for cuttings removal than the Hi-vis mud.
22) Running MWD surveys should be taken every 15 m (can be difficult due to noise) (try at each connection) to check on verticality of casing.
23) Normally 2-3 m of stick-up are left from the 30″ Casing head to seabed.
24) Once the desired stick-up is achieved the string weight is brought to neutral and the casing observed, via the ROV, for 30 minutes for settling. It is advisable to continue circulating during this period (and for step 24.).
25) 20-30 KLBS WOB is applied to the 30″ casing and the casing again observed for 30 minutes.
26) The CART/Drill-ahead is now disengaged by applying slight weight and rotating to the right (3 turns for the CART and a further 2 turns to release the Drill-ahead). Releasing the Drill-ahead may be difficult if cuttings have built-up directly above it. It may be necessary to apply 10-15 kftlbs right-hand torque, work it down then pick-up.
27) The BHA should then be picked up to check the CART with the ROV.
28) Drilling of the 26” hole should start with low flow-rate (1600-1900 lpm) for the first 2 singles, then gradually increased to normal drilling rate (3220 lpm). This reduces the risk of washing out around the 30” shoe.
29) Drill 26” hole using Hi-vis and Bentonite sweeps (40-60 bbls) every ½ stand and prior to each connection or as per Company procedures (Bentonite sweeps have been far more effective at lifting cuttings, and care should be taken not to pack-off the BHA immediately after a Bentonite sweep has been pumped). Each stand should also be back-reamed.
30) Once the 26″ hole section has been drilled to TD, sweep with Bentonite mud, back-ream to the 30” shoe, RIH to TD, spot Bentonite mud in the open hole and 30” casing.
31) POOH and run 20” casing.
Additional:- For 17 ½” Bit, strongly suggest you run a 17 3/8” UBHS, and you may need to be more patient when jetting particularly if the formation becomes competent at very shallow depth, and, you may be required to reciprocate the string more frequently