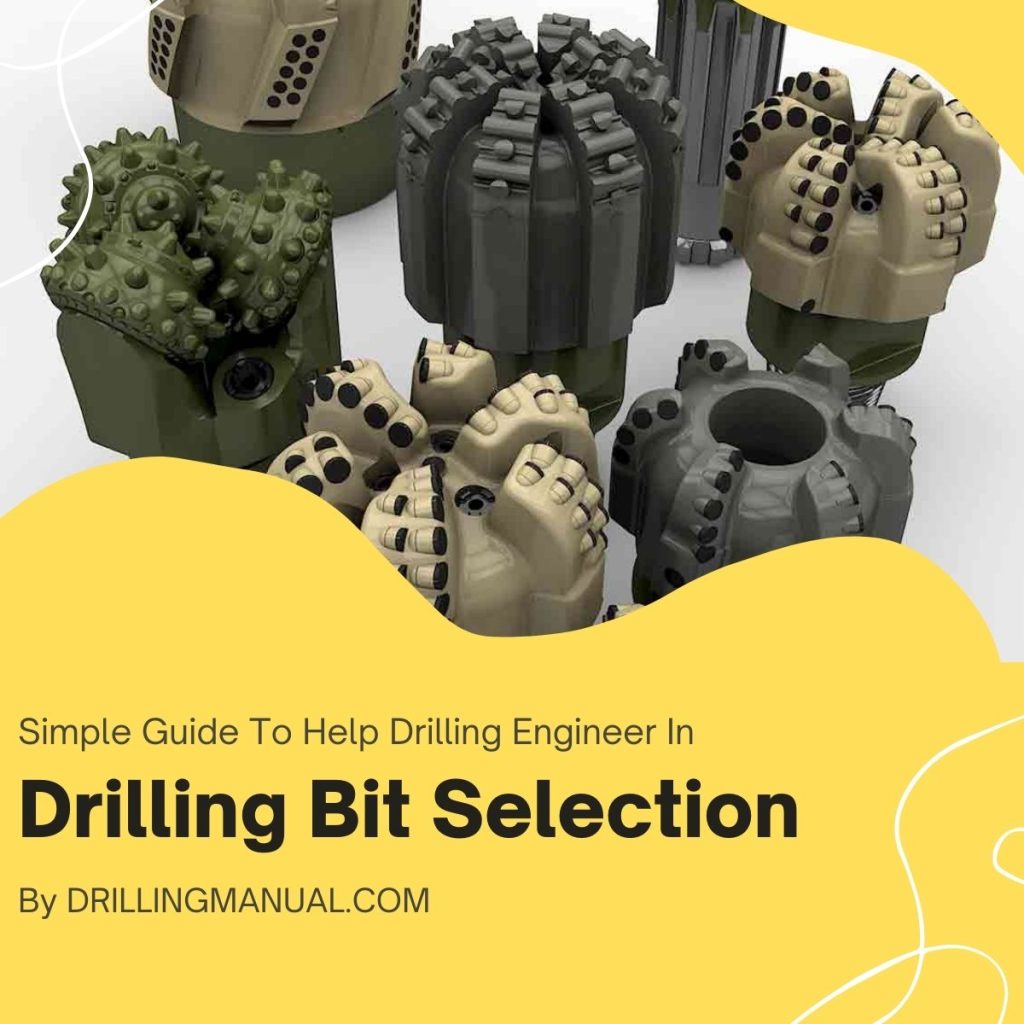
The Importance of Drilling Bit Selection
Optimum ROP and Durability
Drilling Bit selection commonly involves choosing a bit that offers the right balance between durability and Rate of Penetration. We cannot get the maximum penetration rate and durability in one bit. The right balance between the two will yield an Optimum ROP and Optimum Durability for the application.
Avoiding Catastrophe
It is not sufficient to select a bit that offers the desired balance between ROP and durability. We must also be confident that there is little likelihood of significant bit failure. We must be assured that the risk of cone loss through early bearing failure is acceptably low or that an expensive PDC bit will not be destroyed in a hostile formation before reaching its target.
Maintaining Gauge Hole
The bit should be capable of maintaining the gauge hole. If it does not, the next bit will be subject to wear and abnormal loading before it ever cuts fresh formation. It may even be damaged if adequate care is not taken when running in the hole. If the under gauge bit is run at the end of a section, it may be difficult to run the casing.
Directional Responsiveness
The proportion of directional wells being drilled is rising steadily. The complexity of these wells is also on the increase, while the precision required of the well path becomes ever more demanding. The selected bit has to deliver directional responsiveness that will aid the directional driller, not hinder him.
Most directional wells make use of downhole motors. Rock bits must be able to tolerate the higher RPM’s these may deliver, especially when used in conjunction with the top drive or rotary table.
Cutting Structure Integrity
The chosen bit must withstand variations in formation character and applied drilling parameters that might tend to damage the cutting structure. A durable cutting structure may be destroyed very rapidly, even at the start of a run, if the wrong drilling bit selection is made.
Drilling Cost & Bit Selection
So, we have seen some of the critical factors that make bit selection so important. Varied as they are, they have a single thing in common:
Each has a cost. If the selection process is effective, the cost will be minimal. If poor choices are made, costs will rise (also check oil well drilling well cost per foot). Therefore, drilling bit selection is primarily an economic issue, yet, as we shall see, it has little to do with bit price.
The Bit Selection For Drilling Sequence
This is the sequence to be followed in bit selection:
- Define the Objective.(First, we must understand what we want the bit to do, so we define the objective of the application.)
- Gather Data. (we seek out similar applications and gather relevant data.)
- Analyze Actual Performances. (Then, we examine the bits’ performances in these settings, assess the geological data, and set a performance baseline.). (Roller cone bit performance – PDC bit performance)
- Identify Options. (Several options should now be obvious, some of which have been tried, and some of which are suggested by the analysis and by the shortcomings of what has been tried so far. Assess the total costs of each option and select the one offering the lowest cost per foot.)
- Decide based on Probable Cost/Foot.
Defining the Objective
We ask, ‘What do we want the bit to do?’, so we can evaluate bit performances in similar applications. The questions we ask here relate directly to the data we have gathered from offset wells. There are four major areas of interest:
- Lithology
- Interval
- Direction
- Other (Mud, reaming, drill out, etc.)
Lithology In Drilling Bit Selection
What kinds of rock are present? | The fundamental question: the starting point for our inquiries. |
What variations do the rocks exhibit? | Bit performances, as measured by R.O.P., run length, or dull condition, vary considerably, even through rocks that are supposedly the same. Such variations can often be related to differences in lithology. There are limestones, and there are limestones! |
Are the rocks abrasive? | Abrasive rocks are punishing on drill bit conditions. In consolidated, abrasive rocks, PDC bits suffer impact damage, tooth bits wear rapidly, bearing seal life is shortened, and gauge wear is rapid. |
Are they uniform or heterogeneous? | All drill bits benefit from drilling in a uniform lithology. Changes from one rock type to another place stress upon the cutting structure and, in roller cone bits, upon the bearings. In these circumstances, individual teeth, cutters or inserts experience high peak loads. Damaging vibration may be initiated during the transition. |
Compressive rock strength can be derived from log data in several similar ways. The basic requirements are gamma-ray, sonic, and mud logs. The compressive strength of the rock is related to the sonic travel time through a series of equations in which the lithology modifies the constants.
Young’s Modulus of Elasticity | E=[B/Ts2x(3xTs2-4xTc2)/(Ts2-Tc2)]x k x1010 B = Bulk density – log-derived value Ts = Shear Travel Time – calculated with an adjustment reflecting grain size Tc = Sonic Travel Time – log value k = constant |
Clay Fraction | We can determine the shale volume or clay fraction from the gamma-ray values. Again, the constant in the equation is dependent upon the rock character, in this case, the extent of its compaction. Gamma Ray Index Gi = [G – Gc]/[Gsh – G] Shale Volume (Clay Fraction) Equations Cfo = 0.33 x [2(2.0 x Gi) – 1.0] |
Compressive Strength | Armed with this Clay Fraction and Young’s Modulus for the rock, we can compute an in situ compressive strength according to this equation. CS = [a x (1 – Cf + b x Cf )] x E |
The Process | Using a typical Rock Strength Analysis program, we proceed through several steps. From mud logs and wireline data, we select an interval that contains no more than three distinct rock types. We evaluate and quantify the gamma-ray values that distinguish these rock types. The program then examines each data interval, determining the lithology from the limits we have defined for gamma-ray readings, calculating E, Young’s Modulus, clay fraction, and finally, the compressive strength of the rock. The result may then be plotted along with some of the original data. From experience, we know what bit types will be required for particular rock strength values. The peak values encountered, perhaps, only in thin stringers, can be as important as the background values of rock strength. |
Very Low Strength | < 4,000 psi gumbo shales soft shales claystone, loose sands |
Low Strength | 4,000 – 8,000 psi Chalk, argillaceous sandstones, claystone, soft shales evaporites, soft siltstones |
Medium Strength | 8,000 – 16,000 psi Conglomerates, sandy, and chalky limestones marls, medium to medium-hard sandstones, hard shales, evaporites, soft siltstones |
High Strength | 16,000 – 32,000 psi hard stringers, hard dolomites, crystalline limestones, hard (brittle) shales, hard sandstones, soft siltstones |
Very High | >32,000 psi very fine, tight sandstones, chert, quartzite, igneous rocks, metamorphic rocks |
The concept of rock strength computation is a valuable one in the drilling bit selection process. We should be aware of the limitations it suffers from.
The calculated values depend upon the correct lithology identification on a foot-by-foot basis. This, in turn, depends upon the judgment and experience of the analyst. PDC bits are greatly affected by the abrasiveness of the formation. This technique provides no measure of that. As with all offset data, we cannot know how closely the analyzed well, or wells will be in character with the planned well.
Despite this, the data can give us valuable insight into appropriate bit types. Broad guidelines are suggested in this table. The bit selection process in drilling can be improved when combined with the other forms of offset data we shall discuss in the following lecture.
- Light Set 1,000 – 15,000
- Medium Set 10,000 – 20,000
- Heavy Set 15,000 – 30,000
- Ultra Heavy Set 15,000 – 40,000 Diamond 35,000 – 80,000
Direction
We need to know what directional demands will be placed on the bit.
- Will we turn; build; drill a tangent section; drop angle; drill horizontally; or,
- will this be a vertical well?
- Or will there be a combination of some of these well profiles trajectory during the run?
- In addition to what we are doing directionally, we need to know whether our builds or turns are gentle or hard.
- What builds rates will we seek to achieve?
- What will be the dog leg severity?
- Once these facts are established, we must find out how we shall do it.
- The details of the BHA, the mud motor type (e.g., is it low speed-high torque, how many lobes), and the drive type (rotary or top drive) should be determined.
- On directional assemblies, the bend angle of the motor housing is very important – the higher the bend angle, the greater the stresses on the drill bit.
- What proportion of the time do we anticipate sliding versus rotating? (Unwelcome stresses are greater with off-center rotation on a bent housing than when sliding.)
- The combined down-hole and surface rpm are particularly important for roller cone bits as they impact the bearing life. It is also essential for the cutting structure of all bits – high rpm’s in hard formation are often damaging.
Interval
Next, we look at the interval we require the bit to drill. We want to match our selected bit’s durability to the section’s length and difficulty. [The difficulty of the section, in this context, is defined by the other two factors we have looked at – lithology and steering requirement.
Long Intervals | Traditionally we would expect longer intervals to demand more durable bits. An alternative, not considered sufficiently often, is to use more bits. Let’s look at an example. Work through the example. In this instance, using two bits is a less expensive option than one because we gain in ROP more than we lose in durability. The extra trip costs less than the time we save by drilling the hole faster. |
Short Intervals | Shorter intervals can benefit from the use of a more aggressive cutting structure. For example, if an insert bit is pulled short of section TD for some reason – say, rig problems. It could have completed the interval, but it is worn, and we prefer not to re-run it. If the remaining interval is short, we may not need to run back in with the same type of insert but go to a more aggressive one. This will yield a higher ROP, or even to a mill tooth bit, that will be faster and probably less expensive. |
Other Factors
Finally, we look at the miscellaneous category. The miscellaneous tag does not mean the items it contains are unimportant. Sometimes they are vital in drilling bit selection.
Mud Type | Mud type: for fixed cutter bits, this is critical. Many bit designs will not function or function very poorly in water-based muds in particular formations. To properly select a PDC bit, we must know the mud type that will be used. We have seen that run length are rarely long enough for oil and synthetic muds to affect elastomer seal elements but that silicate muds may reduce seal life |
Reaming | Drill bits were not designed for reaming. Reaming loads the bit in a quite different way to drilling on the bottom. This stresses both cutting structures and bearings. We need to know if the bit will likely have to do much reaming in the application, and if so, how hard this will be. With light weights applied, a few meters at three or four points running in the hole is not the issue. We are interested in long, hard intervals that take an extended time to ream. These will take their toll of the bit and reduce its ultimate performance. |
Drill out | Drilling out can be a problem for any bit: non-rotating rubbers rotate, PDCs cannot drill PDC drillable shoes. Be aware of what components will be in the casing string. Select the bit accordingly. |
Junk | How much? What kind? Is it on the bottom? What size? What does it cost us to make a dedicated junk run? What does it cost us if we don’t? If we must, a short-toothed mill tooth bit is the best conventional solution; otherwise, if the problem is severe, a junk mill or generic term – escapes me right now. |
Critical Factors | When we have looked at all these characteristics of the planned well it is time to consider which are critical for this specific application. For example, the key elements in the 17 ½” section might be that we have to build from vertical to 50° over a long interval. |