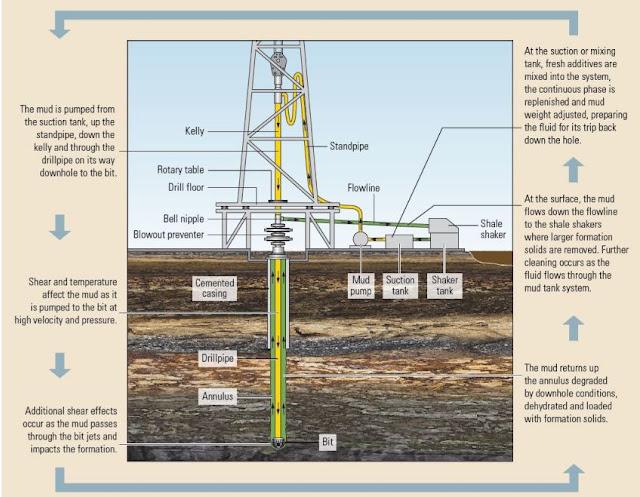
Generally, we must include a complete and comprehensive mud plan in the well-planning process. History has proven that an incomplete mud plan will cost the operator many hours of rig time (also check oil well drilling well cost per foot) and may mean the difference between a productive and a nonproductive well. Here, we shall discuss the functions of the drilling fluids or mud in oil and gas wells.
The use of drilling fluid to remove cuttings from the borehole was first conceived by Fauvelle, a French mud engineer, in 1845. “Drilling fluids” describes a broad range of fluids, both liquids, and gases, used in drilling operations to achieve specific purposes. The fluids may be air, natural gas, water, oil, or a combination of liquids with special drilling chemicals and additives. The main target of Drilling fluids design is to solve or minimize many drilling problems. Therefore, understanding these purposes will help the rig drilling supervisor successfully prepare a mud program, use proper additives, and diagnose trouble areas.
Mud Circulation
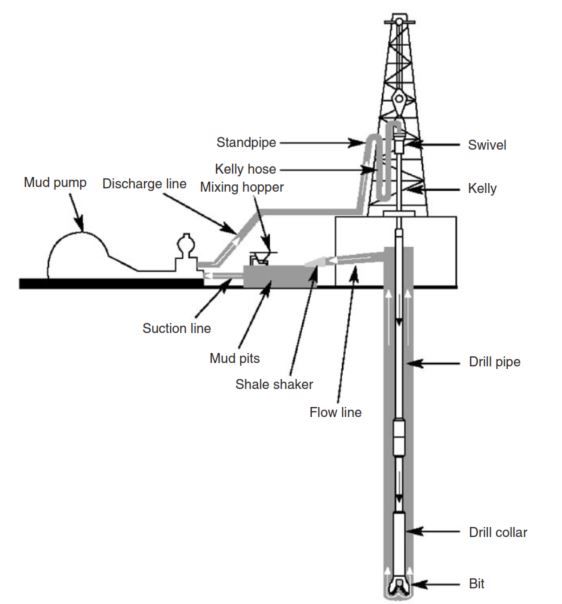
On a drilling rig, we pump drilling fluid from the mud tanks through the Drill String, where it sprays out of nozzles on the Oilfield Drilling Bit. Thus it will help clean and cool the drill bit in the process. The mud then carries the crushed or cut rock (“cuttings”) up the annular space (“annulus”) between the drill string and the sides of the hole through the surface casing, where it emerges back at the surface. A shale shaker or the newer shale conveyor technology will filter the cuttings. After that, the mud returns to the mud pits. The mud pits let the drilled “fines” settle. Also, the pits are where we treat the fluid by adding chemicals and other substances.
The returning mud can contain natural gases or other flammable materials that will collect in and around the shale shaker/conveyor area or other work areas. Installation of special monitoring sensors and explosion-proof certified equipment is essential. This is because of the fire or explosion risks if they ignite. The mud is then pumped back down the hole and further recirculated. After testing, the drilling fluid is treated periodically in the mud pits to ensure there are the desired mud properties that optimize and improve drilling efficiency, borehole stability, and other requirements, as listed below.
Major Drilling Fluids Function
Drilling fluids serve many functions. The major functions of drilling mud include the following:
- Cool and lubricate the bit and Drill String
- Clean the hole bottom
- Carry cuttings to the surface
- Remove cuttings from mud at the surface
- Minimize formation damage
- Control formation pressures
- Maintain hole integrity
- Assist in well-logging operations
- Minimize corrosion of the Drill String, casing, and tubing
- Minimize contamination problems
- Minimize torque, drag, and pipe sticking
- Improve drilling rate
Due to various drilling conditions, we don’t address all drilling fluids’ functions in each well.
It is important to design the drilling fluid program to satisfy the highest-priority requirements for drilling the prospect well. Unfortunately, these requirements may often be conflicting and/or may place demanding constraints on the system. For example, a low-solids system may be desirable for improved drilling rates and minimum formation damage. However, if there will be HP, high-activity shales drilling in an extreme T range, oil muds, or dispersed lignosulfonate systems may be easier to control.
The drilling engineer must attempt to select a system that will achieve the following goals:
- Satisfy the crucial items such as pressure control
- If possible, satisfy all lower-priority requirements
- Avoid using completely unsatisfactory systems.
An example of an unsatisfactory system might be using oil muds in formations that have historically proven nonproductive due to emulsion blockage when oil muds are used.
Drilling Mud Function – Cool and Lubricate the Bit and Drill string.
During the drilling operation, there will be a generation of a considerable amount of heat. Muds can function as a coolant, help transmit this heat to the surface, and lubricate the wellbore. Air bits have special ports that use air circulation within the Bit Bearings for heat dissipation. Note: We are not using air bits in drilling with liquid base mud.
Various additives are available to help lubricate the wellbore. Deep holes or highly deviated wells may require oil or inverted emulsion muds to reduce Torque And Drag from friction.
One Function of Drilling Mud Is To Clean the Hole Bottom.
Removing cuttings from below the bit is one of the most important functions of drilling fluid. The control of Cuttings removal will be by factors such as the chip hold-down effect of the mud, cross-flow of the fluid, fluid viscosity, density of the cuttings, size of the cuttings, the density of the fluid, and fluid velocity (Fig.1).
The chip hold-down phenomenon occurs when the Drilling Bit breaks a chip from the formation. This chip will resist removal and movement from below the bit due to the difference in the hydrostatic pressure of the mud and the formation pressure. To remove this chip, fluids must penetrate beneath the chip.
This feature has been accomplished with drilling fluids that exhibit a high “spurt loss, initial filtration” by helping equalize pressures above and below the chip.
The Task of Drilling Fluid Is To Carry Drilling Cuttings to the Surface.
Transporting the cuttings removed below the bit is a huge and important function of drilling fluid or mud. The fluid velocity in the annulus must exceed the downward falling rate, or slip velocity, of the cuttings (Fig.2). Mud weight, fluid viscosity, suspension, and gelation properties of the mud affect its carrying capacity. Laminar and turbulent flow regimes exhibit different lifting capabilities.
When we stop circulation, the unremoved cuttings must be suspended, or they will fall downward. Suppose mud does not exhibit the proper characteristics to suspend the cuttings. Reentry into the hole and reaching the bottom through the settled cuttings may become time-consuming and costly. However, excessive gellation to suspend the cuttings may require high pump pressures to break circulation, thus increasing the possibility of lost circulation.
Removal of Cuttings from Mud at the Surface.
Removing drilled rock cuttings from the mud circulating system at the surface is mandatory to prevent a high solids concentration buildup (drilling fluid’s function). Mud pits usually do not allow sufficient time for solids to settle out. Mechanical solids removal equipment such as shale shakers, desilters, mud cleaners, and centrifuges has proven its worth in effective drilling. Placement of the solids control equipment in conjunction with the surface circulation system is also very important. Removal of the largest solids should occur near the flow line; we should remove finer solids before entering the suction pit.
Drilling Fluid Can Minimize Formation Damage.
The protection of potential pay zones is important for drilling fluid. The deposition of a filter cake that allows the drilling operation to continue and protects a productive zone is often a forgotten consideration of a mud system. The formation damage is generally a reduction in permeability near the wellbore with perhaps a slight porosity reduction. The problem can be severe in low-permeability reservoirs or with high clay content.
Several mechanisms can cause formation damage during drilling (Fig.3). Filtrate loss from the mud can enter the producing zone and cause interstitial clay swelling, resulting in permeability reductions. We may lose colloidal solids, barite, or clay in the formation, causing a plugging effect. Oil mud filtrates containing emulsifying agents can cause emulsion blockage. These effects can often be reduced in a remedial manner by using acid, mutual solvents, or fracture jobs. Many reservoirs, however, do not respond effectively to remedial methods, which emphasizes the importance of minimizing the original damage.
How Controlling Formation Pressures is a Function Of Drilling Fluid.
Drilling intervals with abnormally high formation pressures require that the function of the drilling mud system can provide sufficient pressures to equal or exceed the formation pressure. The hydrostatic pressure of the mud system achieves this purpose. Insufficient pressure control can cause hole heaving, kicks, and blowouts.
Maintaining Hole Integrity Is One Of The Functions Of Drilling Mud.
Wellbores often exhibit stability problems from geological phenomena such as fractured zones, unconsolidated sections, hydratable clays, and pressured sections. The function of drilling fluid must control these problems so a drilled section remains open and deeper drilling can proceed. Designing a mud system to maintain the integrity of the hole after it has been drilled is often the basis for selecting mud types and properties.
Hole stability problems can usually be grouped into either heaving or sloughing shales. Heaving shale is a mechanical problem, whereas sloughing occurs due to some drilling chemical reaction between the mud system and the formation. We must identify the causes of the hole stability problems before selecting a remedy since solutions for mechanical problems such as mud weight increases will not solve a chemical reaction occurs.
How Drilling Fluid Function In Well Logging.
The physical and chemical properties of drilling fluid may affect the well logging program. For example, a high-salt-content mud may prevent the use of a spontaneous potential (SP) tool since the salt concentration of the mud and formation may be approximately equal. In addition, oil muds inhibit resistivity logs since the oil acts as an insulator and prevents current flow. The selection of an adequate suite of logs must be coordinated with the drilling fluids program to allow proper formation evaluation.
Corrosion of Drill string, Casing, and Tubing.
An increasing number of wells are drilled in formations containing toxic gases such as hydrogen sulfide (H2S). These gases pose health and safety problems to personnel and present dangers to metal components from hydrogen embrittlement, blistering, and stress cracking. The drilling mud system can use additives such as scavengers to facilitate removing these contaminants. In addition, oil muds will minimize corrosion problems, although they do not necessarily reduce health hazards (Oil Rig Hazards).
The Related Contamination Problems To Drilling Fluid Functions.
The mud system must often control various contaminants, including toxic gases, high solids contents, hydrocarbon gases, and ionic contamination. Mud types commonly used in the drilling phase have varying abilities to control these contaminants. For example, a dispersed lignosulfonate mud has a high solids tolerance, whereas some polymer systems function poorly with even small concentrations of solids. Drilling environments must be evaluated when developing the well plan & drilling program to allow for selecting the proper mud system to control possible contaminants.
The Duty Of Drilling Fluids To Minimize Torque, Drag, and Pipe Sticking.
Excessive Torque And Drag are problems commonly encountered in drilling operations that can be addressed by selecting the proper mud system and additives. Torque is the force required to rotate the Drill String. Drag is the incremental force above the string weight required to move the pipe vertically. Excess torque can cause drill string twist-off, while high drag forces can cause pipe sticking and pipe parting.
One of the functions of a drilling mud system is to reduce the severity of torque and drag problems. If the problems occur due to formation hydration and swelling, certain chemicals or mud types will inhibit the formation. As a minimum effort, we can use lubricants to reduce the friction coefficient along the walls of the wellbore.
Pipe sticking is a costly problem we can avoid by proper mud system maintenance and selection. Differential Stuck Pipe occurs when the pipe becomes embedded in the filter cake opposite a permeable zone and is held in place by the difference between hydrostatic and formation pressure (Fig.4). Low water loss muds can reduce the frequency and severity of the occurrences. In many cases, oil muds will virtually eliminate the problem.
The Last Drilling Fluid Function Is To Improve Drilling Rate.
There are a lot of factors affecting the drilling rate & it is also affected by various properties of the mud system. High-viscosity muds reduce the cross-flow velocity beneath the Drilling Bit, which inhibits cuttings removal. Lower water losses and high solids content retard equalization of pressure around the drilled chip, requiring regrinding before removal. The mud selection function to optimize drill rates can reduce the drilling time. However, caution must be exercised so other problems do not occur, such the formation damage, hole stability, or Stuck Pipe.
Thanks for the content but it should be improved by making functions more brief
Ok We will enhance this