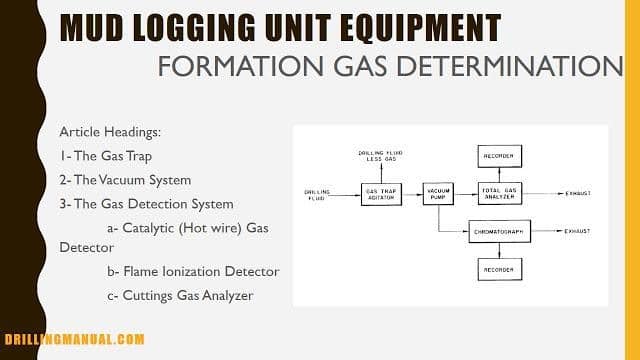
This article is one of 5 important articles about Mud logging unit equipment. These articles explain in detail the equipment used in standard mud logging units to detect drilled gas.
Surface logging is performed using the returning mud stream to communicate with the bottom of the borehole. There is a general relationship between the kind and amount of hydrocarbons in the drilling fluid arriving at the surface and the hydrocarbons in the formation as it was drilled, with that portion of mud passing across the bottom.
If the gases are present, they are released from the cuttings into the mud stream and entrained, probably in solution, in the drilling fluid. At the surface, it is necessary to remove and detect these hydrocarbons. To do this, the following equipment is used:
- A gas trap that continuously samples the drilling fluid and simultaneously removes gases from the fluid
- Equipment to transport and regulate the air-gas mixture from the trap to the detector in the logging unit
- Gas detector and chromatograph, which process the air-gas mixture into concentration and compositional gas readings
The Gas Trap
To meet the unique requirements of surface logging, the gas trap must perform the following important functions:
- extract gases contained in the drilling fluid, independent of such variables as density, viscosity, and gel strength of the mud
- sample consistently, regardless of the flowrate through the circulating system
The gas trap consists of a steel box or cylinder that sits in the mud ditch (as near to the flowline exit as possible but before the shakers) and allows the drilling fluid to continuously pass through it employing a hole in its base. An agitator motor sits on top of the gas trap and has a propeller shaft extending into the mud. The propeller continually agitates the drilling fluid as it passes through the trap. A continuous flow of air enters through a vent in the top of the trap and is whipped through the mud where the maximum mud surface is exposed. It is this air-gas mixture that is subsequently drawn into the logging unit.
The Vacuum System
After the gases are removed from the drilling fluid, they are transported to the gas detector in the logging unit. This is accomplished using a vacuum pump connected to the trap by a hose length. Through this hose, the pump pulls a continuously measured stream of sample gas through the vent in the trap. Formation gases, if present, are continuously extracted from the drilling fluid in the gas trap and are mixed with air and carried into the logging unit via a condensate bottle, where water vapor is extracted. The flow of air, or air-gas mixture, passes through additional flow-regulation equipment, plumbing, and instruments and arrives at the detector where a continuous gas reading is obtained.
The Drilled Gas Detection System
1. Catalytic (Hotwire) Gas Detector
This instrument uses the principle of catalysis (i.e., the catalytic oxidation of gases on a filament in the presence of air). It is an application of the Wheatstone bridge measuring circuit, in which a resistance (the detector filament), will vary according to the drilled gas concentration and is compared to a fixed standard (the reference filament). The reference filament is coated with an inert compound to seal the surface from the atmosphere, and the imbalance is measured. When a voltage is applied across the entire bridge, both filaments are heated sufficiently to oxidize all gaseous hydrocarbons.
Before the gas detector is placed in operation, it is calibrated using air as a standard. A valve (zero adjust) is opened to admit fresh air to the system, which places both filaments in a like atmosphere (the gas concentration is zero). By adjusting the “Zero” potentiometer, the gas meter, a sensitive milliammeter, is adjusted to read zero. Electrically, the gas detector is then said to be “in balance”. The Zero Adjust valve is then closed, exposing the filaments to whatever atmosphere is created in the gas trap.
As long as no drilled gas is being liberated from the mud, the filaments remain in an air atmosphere, and the detector reads zero. However, as soon as any gas from the mud becomes mixed with the air being drawn through the detector, the filaments are surrounded by this atmosphere. Having free access to the detector filament, the mixture oxidizes. The oxidation creates heat; the detector filament temperature increases (increasing resistance); the electrical balance is upset, and current flows through the milliammeter. The greater the gas content present, the greater the electrical imbalance, and the resultant gas reading will increase.
To qualify the drilled gas reading, a known concentration of combustible gas, usually methane at 1% by volume in air, is passed over the filament, and the gas reading is adjusted to reflect the concentration. Older-style gas detectors may display gas concentration in “units”. Unfortunately, various surface logging companies use different definitions of what concentrates a “unit”. Traditionally, EXLOG/INTEQ has used 50 units to equal 1%. In addition, the FEL log heading should explain the calibration gas used to determine the gas unit.
Because of the varying values of the term “unit”, it is common to report gas readings on the FEL in terms of percent methane-in air, or parts per million (ppm), so that well-to-well comparisons can be made of gas readings.
In the catalytic system, if the drilled gas concentration exceeds 2 percent, the mixture must be diluted so that the readings remain “on-scale”. This is accomplished by introducing dilution air into the air-gas mixture. This dilution air is controlled volumetrically by flowmeters. When the volume of the air-gas mixture is reduced by one-half, the scale of the milliammeter (and the recorder) is effectively doubled, and the gas reading shown must be multiplied by two.
2. Flame Ionization Detector (F.I.D.)
This system uses a continuous sample fed into a regulated, constant-temperature hydrogen flame. The flame is situated between two electrodes in a high potential (300 volts) atmosphere. As combustion occurs, the gas ionizes into charged hydrocarbon residues and free electrons. A predictably constant ratio of these charged particles moves immediately to the positive electrode (anode), inducing a current at that probe. The amount of current induced is proportional to the total ion charge produced in the flame and increases as the percentage of hydrocarbons in the sample increases. The ion charge measures the total number of carbon-hydrogen bonds in the air-gas mixture.
The FID detector meter displays the percentage of methane equivalent (C1) hydrocarbons in the drilled gas sample. It is calibrated to read 1.00 when a 1% methane calibration gas burns in the FID. When burning a ditch sample containing heavier hydrocarbons (those with a greater number of carbon-hydrogen bonds in the molecular structure than in methane), the meter displays a reading reflecting the proportionately greater number of carbon-hydrogen bonds.
For example, when burning a 1% concentration of pentane (C5), the meter reads 5.00; when burning a 2% pentane or a 10% equivalent methane mixture, the meter reads 10.00 (2% pentane = 2 x 5 =10 carbon-hydrogen bonds; 10% methane = 10 x 1 = 10 carbon-hydrogen bonds). Each of these readings indicates that the relative concentration of combustible hydrocarbons is 10 times greater than that in the calibration gas.
3. Cuttings Drilled Gas Analyzer
This detector checks the number of combustible hydrocarbons in the drilling mud and drill cuttings. It differs from the ditch gas analyzer because it is a batch system. Samples of the drilling fluid and cuttings are collected and checked periodically (always during any ditch gas show). These samples (approximately 200 ccs, but always a consistent amount) are placed in a blender jar and agitated for a standard time. The resultant air-gas mixture is drawn into the gas detector.
The gas combustion, air dilution, millimeters, voltmeters, and flowmeters are all identical to (and are employed in the same manner) those in the catalytic ditch gas analyzer. However, since this is a batch system, no recorder is used, and the gas readings are read directly from the milliammeters as gas units/ percent.
The blender gas results are used on prospective gas wells to check the ditch gas analyzing system. On prospective oil wells and wildcat wells, the cuttings gas is extremely important as it may form the basis for further evaluation as an indicator of reservoir porosity and permeability.