Casing pipes are robust and durable tubes made from different materials, such as steel or PVC, designed to provide structural support and protection to the wellbore or borehole. They are inserted into the drilled hole and cemented in place, forming a protective barrier that prevents the collapse of the well walls and the contamination of underground water sources. In this article, we shall discuss the major casing applications, types, sizes, grades & specifications in detail.
Casing pipes come in various sizes and wall thicknesses, allowing for customization to meet specific requirements. For instance, some pipes may need to be thicker if the soil is prone to collapse or if the drill pipe needs extra support. We also use steel casing pipes extensively in underground construction projects requiring a durable and resistant material.
Casing Pipe Applications
Casing pipes are placed in a wellbore for the following reasons:
- Supporting the weight of the wellhead and BOP stack.
- Providing a return path for mud to surface when drilling.
- Isolating high-pressure zones from the wellbore.
- Controlling well pressure by containing downhole pressure.
- Isolating special trouble zones that may cause hole problems, e.g.:
- Swelling clay, shales.
- Sloughing shales.
- Plastic formations (evaporites).
- Formations causing mud contamination, e.g., gypsum, anhydrite, salt.
- Frozen unconsolidated layers in permafrost areas.
- Lost circulation zones.
- Separating different pressure or fluid regimes.
- Isolating permeable zones from the wellbore will likely cause differential sticking.
- Providing a stable environment for well packers, liner hangers, etc.
- Isolating weak zones from the wellbore during hydraulic fracturing.
- Confining produced fluid to the wellbore and provided a flow path to the surface.
- Isolating permeable productive formations reduces the risk of underground blowouts.
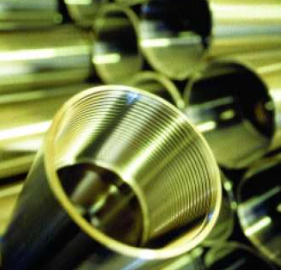
Production casing must perform several critical functions as follows:
- Providing internal pressure containment when the tubing system leaks or fails.
- Preventing wellbore fluids from contaminating production.
- Protecting completion equipment.
- Providing access to producing formations for remedial operations.
- Providing cement integrity across producing formations.
Casing Pipes Profiles & Types
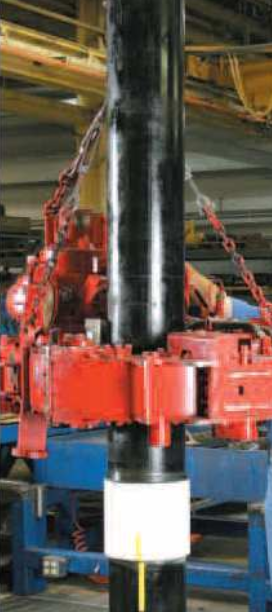
The following are the various casing types & configurations that can be used for onshore and offshore wells.
Onshore Wells
- Drive/structural/conductor casing
- Surface casing
- Intermediate casing pipes
- Production casing
- Intermediate casing and drilling liners
- Intermediate casing and production liner
- Drilling liner and tie-back string.
Offshore Wells – Surface Wellhead
As in onshore above.
Offshore Wells – Surface Wellhead & Mudline Suspension
- Drive/structural/conductor casing
- Surface casing and landing string
- Intermediate casings and landing strings
- Production casing
- Intermediate casings and drilling liners
- Drilling liner and tie-back string.
Offshore Wells – Subsea Wellhead
- Drive/structural/conductor casing
- Surface pipes
- Intermediate pipes
- Production CSG
- Intermediate CSG and drilling liners
- Intermediate CDGpipes and production casing liner
- Drilling liner and tie-back string.
Casing Specification Parameters
Typically, By using five parameters, we can determine the casing pipe specifications. These parameters are size, length range, nominal weight, grade & coupling types.
- Size.
- Length Range
- Nominal Weight / Weight per unit length
- Steel Grade
- Coupling Types
The First Casing Specifications Parameter is The Casing Sizes
There are three types of Casing Size designations
- Outer diameter: is the diameter from the outer wall across to the outer wall. In addition, it is the diameter measurement casing is identified with.
- Inner diameter: measured from the inner wall to the inner wall.
- Drift diameter: this is the guaranteed minimum diameter of the CSG. The drift diameter is critical because it indicates whether it is large enough for a specified bit size to pass through.
The Length Range
API has established three length ranges for casing pipes with limits and tolerances, as shown below. API specifications for casing and tubing designate the length range of each joint. There are three length ranges for casing (R1, R2, R3):
The most common length range for casing pipes is R-3 lengths. These longer lengths reduce the threaded connections needed for the casing string. Since we usually run casing in single joints (instead of doubles or triples), the longer R-3 lengths are easier to handle.
API Casing Pipe And Tubing Weight Designation
Casing and tubing weights are one of the specifications expressed in lb/linear ft and are designated as either plain end weights or nominal weights.
- Plain-end weight per foot is the weight per foot of the pipe body, excluding the threaded portion and coupling.
- Nominal weight per foot is the weight per foot that is reflected in casing tables and is an approximate average weight per foot of the pipe with API connections, including upsets, threads, and couplings.
- The average weight per foot is the total weight of an average threaded pipe joint with one coupling divided by the total length of the average joint.
By knowing the outer and inner diameter of the pipe and the density of steel (489 lb/ft3), we can calculate the plain end weight of casing pipes:
The difference between nominal weight and average weight is generally small and most design calculations will depend on using nominal weight per foot.
Casing Pipes Grades
We generally identify steel casing grades by letters and numbers, which indicate various characteristics of the Casing steel (for example, P110). It is a specification according to its yield stress, ultimate tensile strength, chemical composition, heat treatment, or other characteristics. Many grades of casing steel pipes make up oilfield tubulars.
API Casing Pipes Grades For Any Size
The steel grades of joint oilfield API-5CT casing include J55, K55, N80-1, N80Q, and P110. To understand API CSG grades, it is essential to understand the terms minimum yield stress, maximum yield stress, and minimum ultimate strength. To explain these terms, we will use two popular grades of oilfield tubulars as an example: L-80 and N-80.
The Steel casing pipes grade is denoted by a letter of the alphabet followed by the minimum yield stress of the particular steel. For example, the API P-110 has a minimum yield stress of 110,000 psi, and the API grade L-80 has a minimum yield stress of 80,000 psi, as shown by point “A” in Figure 2. In other words, it can support a stress of 80,000 psi with an elongation of
0.5%.
The ‘L’ is a distinguishing prefix to avoid confusion between steel grades. The letter in conjunction with the number, designates such parameters as the maximum yield strength and minimum ultimate yield strength.
Example
In L-80, point ” B ” shows the maximum yield strength as 95,000 psi, which is 15,000 psi higher than the minimum yield stress. Point ” C ” shows The minimum ultimate strength as 95,000 psi. Note that there is no maximum ultimate strength specified.
N-80, another API grade (see Figure 3), also has a minimum yield stress of 80,000 psi but is different from L-80 in that the former has a more significant maximum yield stress of 110,000 psi (shown by point “B”).
This is 30,000 psi higher than the minimum yield stress and twice the tolerance of L-80. The minimum ultimate strength of 100,000 psi is also higher, as shown by point “C”. Whereas N-80 has no hardness specification, L-80 has a hardness specification of 23 HRC. The tight tolerance on yield strength and hardness allows the L-80 to be more suitable for H2S service than the N-80 grade tubulars.
Non-API Casing Pipes Grades For Any Size
The steel industry uses grades other than API grades with unique properties such as high tensile strength, collapse strength, or sulfide stress cracking resistance. These grades are widely used for specific applications.
This pipe is manufactured to many, but not all, of the API specifications with such variations as steel grade, wall thickness, OD, threaded connection, and related upset.
As a result of these changes, the ratings of internal yield, collapse, and tension for both the pipe and the connection are non-API.
When evaluating proprietary products, they are generally assessed using API formulas or in compliance with API methods. Furthermore, parameters such as drift diameter, wall thickness tolerance, length range, and weight tolerance are either determined using API specifications or maintained by them.
Casing Connections For Any Sizes & Grades
- API connections:
- Round Thread: Short, STC or Long, LTC
- Buttress Thread, BTC (also,“BCN”)
- Extreme Line Thread, XL (integral connection)
Premium Connections (Proprietary Connections):
- Hydril
- Manesman
- VAM
- Etc.
In this Casing Connections article, we explained API & Premium connections in more detail.
Casing Design
The design is actually a stress analysis procedure. In addition, the objective of the procedure is to produce a pressure vessel that can withstand a variety of external, internal, thermal, and self-weight loading while at the same time being subjected to wear and corrosion.
In the Casing Design Calculations article, we have gone deeper through the design calculation process.