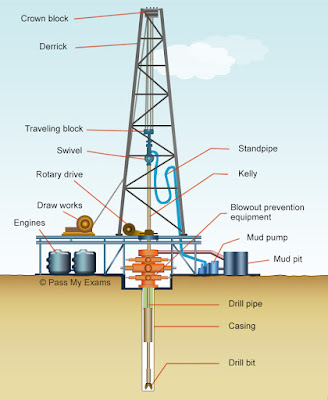
Points to be checked before rig acceptance
1. Weld 30” riser (weld two x 3” valves on the bottom of the conductor casing to be used to take a return to the caller if required, check the conductor for any junk inside before welding.
2. Install the cellar jet and function test it (fill the cellar with water and drain it to the waste pit with cellar jetting).
3. Make sure all the clamps for all high-pressure lines are installed.
4. Ensure that the fall arrestors below the drill floor are installed for work on BOP stack’s.
5. Install the flow line and leak test the same.
6. Install centrifuge frame on mud system.
7. Make sure all eye wash stations are working well.
8. Install emergency shower; function test same.
9. Prepare the PPE for mixing the hopper and have it in place close to the hopper.
10. Install water hose on mud system for derrick man to use inside mud lap.
11. Prepare the required amount of hi-vis pills & spud mud as per the program.
12. Have the two air pumps in good working condition and ready to use before rig acceptance.
13. Have the high-pressure washing machine working and ready for use.
14. Start the pump for cutting ditch blow shale shakers and keep water circulating.
15. Start the water transfer pump at the water pit, and fill the drill water tank.
16. Install a barrier around the water pit and the warning sign.
17. Remove the junk from the location entrance.
18. Install a water hose on the rig floor and ensure it works.
19. R/U easy TQ and function test same.
20. M/U bit sub (Drilling Subs) (C/W float and Totco), 1 x 9 ½” D/C if required, hang it on blocks for an alignment check.
21. Prepare BHA on racks as per the given instructions.
22. Function test mud pumps relief valves (each one to be tested separately).
23. Connect the ECS network cable from the unit to the drilling supervisor‘s office.
24. Ensure the fire hose is installed, the proper nozzle is available, and the hose is long enough to reach the fairest point on the rig site camp (welder workshop).
25. Test fire alarms from the rig floor.
26. Test the emergency shutdown system.
27. Ensure all firefighting equipment is in place and ready to work.
28. Test air hoists for holding weights without slipping.
29. Test crown o-matic.
30. Function test all solid control equipment.
31. Check that all rig engines are working together and see on the rig floor panel.
32. Prepare the rescue at height kit on the dog house.
33. Install the driller (Check also Driller Job Descriptions) protecting the metal frame.
34. Weld a box on the dog house for the first aid kit and put it in place.
35. The doctor to check that the first aid kit contains all necessary components.
36. Make sure all air compressors are working and delivering air pressure of 110-120 psi while the two air hoists are working.
37. Install casing stabbing board and function test same.
38. Install pup joint inside BOP’s and prepare it for testing.
39. Connect hydraulic lines to the BOP stack and the BOP control unit as the surface hole is short, and there is not enough time to cont R/U after rig acceptance.
40. Make sure all earthing cables in place and connected to the conduction pipe (don’t forget earthing cables for ECS and cement units).
41. Make sure that cat head is delivering the proper TQ (minimum 7000 lbs – tong pull).
42. The camp boss will prepare the main camp for acceptance and ensure that everything is okay as per your company galley and accommodation checklist.
43. Check the Kelly spinner; ensure it works on both sides.
44. Ensure the trip tank pump is working in good condition.
45. Check all the safety pins for all shackles on the rig floor (use the proper type).
46. Check the safety pins for the drill collar and pipe slips to avoid dropping segments in the hole.
47. Prepare spider slips and rig elevator.
48. Check the availability of backup hoses (choke, Kelly, and jumper hose).
49. Prepare snatch blocks on the rig for check.
50. Separate dangerous chemicals, isolate it, and install a safety sign in front of it.
51. Distribute enough garbage cans around the location.
52. General housekeeping around the location.
53. Make sure that the BOP test pump working the chart works well and that you have the chart papers.
54. Make sure all the pressure gauges for all the solid control equipment are in good condition and change the damaged ones.
55. Test the vacuum degasser and ensure it achieves the required drawdown.
56. Ensure that the rig derrick scab line is installed, the end is covered with sand, and the way is clear of obstructions.
57. Make sure that both master points are clear of any material. T cardboard is updated and ready for use.
58. Ensure all wind socks on the rig floor and mud system are installed before rig acceptance.
Required Certification Before Acceptance
Senior Tool Pusher to prepare the following certificates and submit them to the company representative before Rig Acceptance for check:
1. Bop’s certificate.
2. Certificate for easy TQ sling.
3. Certificate for M/U and Break out lines.
4. Certificate for traveling block, hook.
5. Certificate for swivel and all Kelly components.
6. Certificate for all BHA components.
7. Certificate for the crown block.
8. Certificate for all rig floor slings (tong backup slings, tong hanging slings, air hoist slings).
9. X-Ray and MPI certificates for standpipe manifold.
10. Inspection certificate for the modification on poor boy degasser.
11. Certificate for deadline anchor.
12. Inspection certificates for sheaves hung on rig mast (Man riding sheave, sheaves for two air hoists.
13. Inspection reports for BOP crane.
14. IWCF certificate for (4 drillers, two night pushers, and two senior tool pusher).
15. Certificates for the rental crane (crane certificate, driver certificate, sling certificate): make sure that the digital weight indicator is working, the tires are in good condition, and the back alarm is working with good sound.
16. Complete the lifting register.
17. Complete the high-pressure hose register.
18. Inspection reports for all the lifting points for (pipe baskets, caravans in rig site and camp side, engines, SCR, workshop, water tanks, poor boy degasser lifting bad ayes, mud lap, and diesel tanks——————-).
19. Inspection for all lifting bad ayes in mast, substructure, and substructure extensions set back area lifting bad ayes.
Safety engineer to supply the following before rig acceptance:
1. Prepare a register for a safety harness.
2. SJA for rescue at height.
3. Ensure all smoke detectors work on the entire caravan in the rig site and main camp.
4. Updated training matrix.
5. To follow up with the office about the status of the ordered safety signs.
6. Safety engineer to prepare a drill register for all the drills performed in both rig site and cam site.
7. Digital copy of the hazard area map (Oil Rig Hazards) for horizontal and vertical views.
8. Check the inspection date of the automatic fire fighting system for SCR and kitchen is valid before rig acceptance.
9. Check all the breathing equipment and get it ready (inspection reports for the bottle’s body should be available and valid).
10. Prepare a training program for the catering crew for fire fighting, record names in the attendance sheet, and keep these sheets on file.
Note:
** BOP’s to be tested on the stump and choke manifold also to be tested before time for N/U.
** Well control equipment to be ready and tested before BOP N/U.