Schlumberger provides three types of PowerDrive RSS or rotary steerable systems with different principles of operation, and different generations of tools exist within some of these groups. The division of systems is as follows:
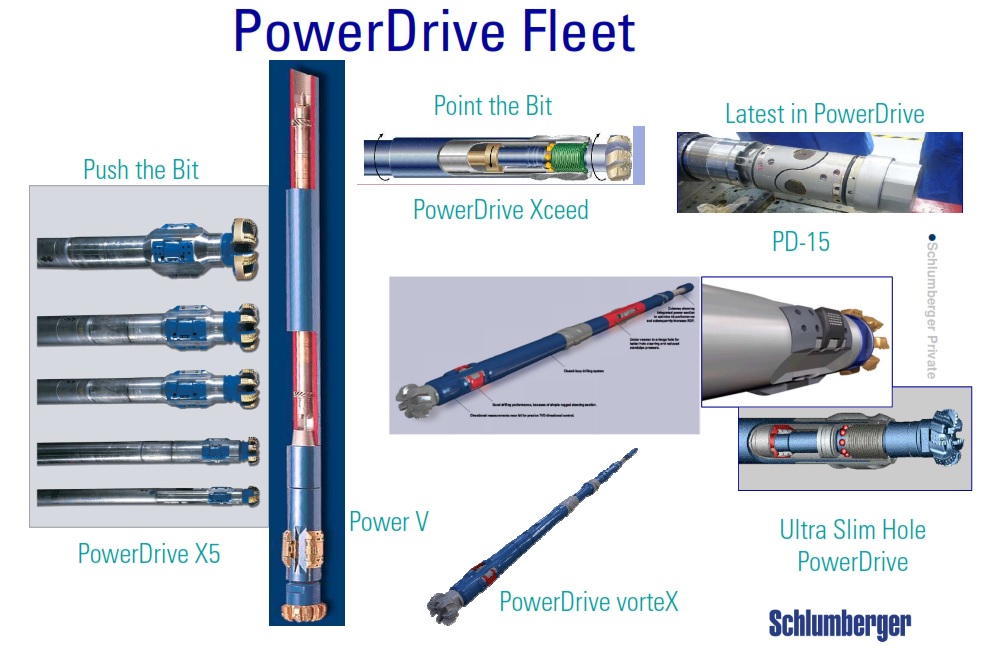
- Firstly, PowerDrive Xtra, PowerDrive X5, PoweDrive X5R
- Secondly, PowerV – vertical drilling system
- Thirdly, PowerDrive Xceed – Schlumberger Point-the-bit RSS
- Fourthly, The PowerDrive Xbow
- Fifthly, PowerDrive Orbit – Push-the-bit RSS
- Sixthly, The Powerdrive Xcel
In addition to the above rotary steerable systems, a fourth service combines PowerDrive technology with an integrated motor power section.
- PowerDrive vorteX – PowerDrive + integrated motor power section.
All these Schlumberger rotary steerable systems have one feature in common that is unique in the marketplace today. Their design is to fully rotate all external components exposed to the annulus at the same speed as the drill string. (or motor bit box should incorporate a power section above the rotary steerable, i.e., PowerDrive vortex configuration). We can summarize the advantages of a fully rotating system as follows.
- Less friction with the borehole wall.
- More efficient cuttings & solids removal.
- Also, Less chance of becoming mechanically stuck or differentially stuck.
- In addition, Less chance of drilling a spiral hole.
- Furthermore, it Reduced interference through casing shoes, windows, and across whipstocks.
- Lastly, More transparency to the drilling operation, e.g., more compatibility with reaming operations.
Schlumberger Powerdrive XTRA, Powerdrive X5
These Schlumberger RSS systems consist of four main components.
- The Bias Unit consists of an internal rotary valve controlling the hydraulic actuation of three externally mounted pads – Purely Mechanical; it provides bit deflection.
- The Control Unit is a geostationary electronics package mounted within the Schlumberger rotary steerable system collar – Electronics, control of TF, and steering percentage.
- A Stabiliser acts as a third point of borehole wall contact for directional control. Selecting the option of string, integral blade, or sleeve-type stabilizers allows the position and size to be varied to fine-tune the behavior in different environments.
- An optional Flex Joint can be used to increase the dogleg capability of the system.
Schlumberger RSS Principle Of Operation
The Control Unit, mounted inside a Control Collar, derives power from the flow of drilling fluid across an impeller. It houses the control electronics and directional instrumentation required to control the tool’s behavior and can hold itself stationary inside the rotating collar. Attached to the downhole end of the Control Unit is a control shaft. This runs down into the Bias Unit.
When the Control Unit is stationary, so too is the control shaft. A valve on the end of this rod seats over three ports that rotate along with the rest of the Bias Unit. As the ports pass underneath the stationary valve, drilling fluid is diverted into them. The fluid then activates each of the three pads, so they always push out at the same relative position in the borehole. The action of the pads on the same point of the borehole wall forces the bit in the opposite direction. The time the Control Unit is stationary over a given period determines the tool’s dogleg capability.
Communication with the tool to change steering direction and strength is achieved by executing combinations of flow rate changes at the surface.
Schlumberger Rotary Steerable System Features
- Rated to 125°C
- Dogleg capability up to 8°/100ft
- A real-time link to MWD (Measurement While Drilling) is available for Near Bit Inclination, Azimuth, and tool status information.
- Stabilizer size and placement options, i.e., stabilized control collars
- Max RPM 220
Schlumberger PowerDrive X5 Features
- As above, but rated to 150°C
- Azimuthal Gamma Ray for Near Bit data in four quadrants
- Cruise Control provides automatic inclination hold, i.e., downhole closed loop functionality.
- Ruggedized and simplified Bias Unit and Control Unit design.
PowerV – Principle Of Operation
PowerV operates on the same principle as Schlumberger PowerDrive Xtra and PowerDrive X5. However, its design target is drilling vertical holes only. It maintains a vertical hole by automatically correcting for any deviation from the vertical.
The system is fully rotating, even when performing corrections. The system has the following advantages and confers the usual benefits of rotary steerable drilling.
- We can apply more weight on bit without fear of building an angle.
- The removal of the need for time-consuming sliding intervals or correction runs.
- There is no need for any interaction from the surface to maintain vertical drilling.
- We can run the system stand-alone, i.e., without MWD tools.
PowerV Features
- 150°C rating.
- Automatic closed-loop vertical drilling.
- We can run it below a motor power section (PowerDrive vorteX configuration).
Schlumberger PowerDrive XCEED – RSS
PowerDrive Xceed operates on a point-the-bit principle. It comprises three internal modules and a collar. Unlike Power Drive, all internal and external parts rotate at the same speed as the drill string.
- The collar has two threaded shoulders for the mounting of variable-size sleeve stabilizers. Along with the drilling bit, these provide the three points of contact that determine directional response.
- The Power Generation Module uses Power Pulse MWD technology to generate tool power from the flow of drilling fluid over a turbine.
- The electronics contain an MWD-type directional package and control systems for the tool’s operation.
- The steering section orients an offset bit shaft to provide a toolface offset at the bit that determines the direction in which the hole is drilled.
Schlumberger RSS system – Principle Of Operation
The bit shaft is connected to an electric motor slightly off-center from the tool axis in the steering section. This results in an offset at the bit box and, thus, at the bit itself. To hold a given toolface, the motor is rotated at exactly the same speed as the collar but in the opposite direction. The net result is that the bit shaft offset remains stationary relative to the borehole. PowerDrive Xceed will then drill in this direction. The time the offset position is constant over a given period determines the tool’s dogleg capability. Drill string RPM, torque, and weight are transmitted through the collar and into the bit shaft just above the bit box by a universal joint arrangement. The tool’s internal components are thus protected from the forces generated by the drilling process.
Communication with the tool to change steering direction and strength is achieved by executing combinations of flow rate changes at the surface.
Steering Control
- The collar supplies drilling torque directly to the bit shaft.
- The bit shaft has a fixed offset from the axis of the collar (eccentric)
- DC motor holds offset toolface geo-stationary by rotating at collar rpm in the opposite direction
- Three points of contact provide the steering tendency.
- The tool has two modes while drilling:
- – Steering Mode: Toolface is held geo-stationary
- – Straight Mode: Toolface indexes at 112.5° / 10 s
- Dog Leg capability is varied by changing mode timing.
Schlumberger RSS Applications
PowerDrive Xceed’s method of operation results in it being very well suited to certain applications. These are:
- High dogleg capability in unconsolidated or interbedded formations.
- Open hole sidetracking.
- Drilling & steering with a bi-center bit.
- Drilling in tough or abrasive environments.
- Full-back reaming capabilities.
- Reduce stuck pipe potential.
PowerDrive Xceed Features
- Rated to 150°C
- Max RPM 350
- Dogleg capability up to 8°/100ft
- Real-time link to MWD for Near Bit Inclination and Azimuth and tool status information.
- Stabiliser size options
- Cruise Control provides automatic inclination and azimuth hold, i.e., downhole closed loop functionality.
VORTEX – Schlumberger Rotary Steerable System
PowerDrive vorteX combines an integrated motor power section with PowerDrive systems. Combining these two technologies results in higher, more consistent bit RPM and smoother power delivery. The following benefits to the drilling process can be realized.
- Increased penetration rates
- Reduced stick-slip
- Reduced casing and drill string wear
- Rotary steerable usage on power-limited Drilling rig Types
Schlumberger PowerDrive RSS References:
- SLB Vortex System
- SLB Xceed
- Shell Directional Drilling Manual
- Schlumberger RSS Orbit System