Flowing wells equipped with a single tubing string are usually completed with a packer. Single-zone completions may involve the downhole commingling of production from several intervals within that zone. Examples of single-zone completions are shown in Figure 1.
At the design stage, optimum tubing size for maximum long-term flow rate, future artificial lift needs, and future workover operations should be considered.
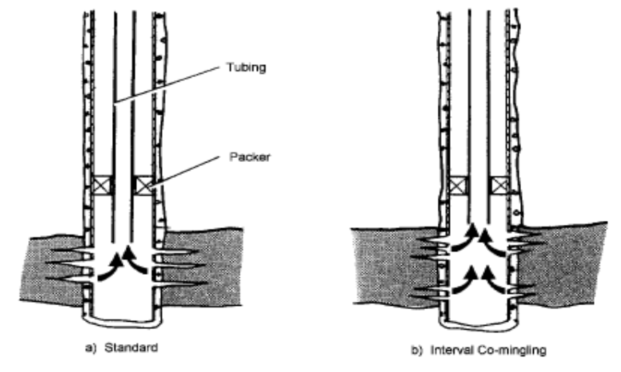
Tubingless Casing Flow.
In this single zone completion type, We produce the hydrocarbons through the casing. Yes, it is a low-cost option. However, it is not without its disadvantages. Firstly, the production casing may be of such a diameter that the flow area is so large that the superficial fluid velocities are low enough for phase separation and slippage to occur, resulting in unstable flow and increased flowing pressure loss in the casing. To be effective, this approach is only applicable to high-rate wells. Secondly, the fluid is in direct contact with the casing, which could result in casing corrosion, erosion, or potential burst on the casing at the wellhead if the well changes from oil to gas production.
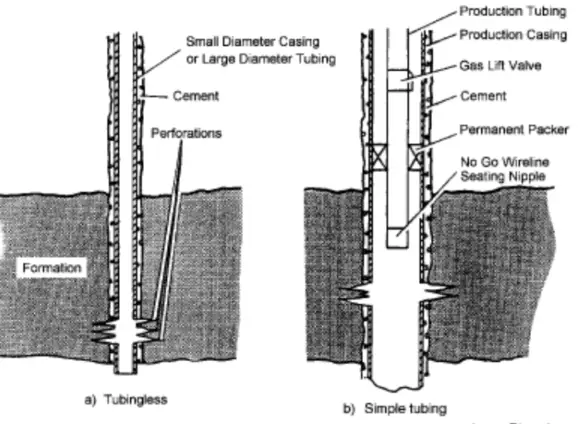
Tubingless single-zone completions are potentially hazardous, especially in offshore installations, as there is an increased risk of collision damage offshore and no facility to install sub-surface safety valves (SSSVs). The use of casing flow production methods has been discouraged both offshore and onshore but is under review again due to potential cost savings and the availability of new equipment.
When there is a plan for a workover, the first requirement is to kill well. In this completion, the reinstatement of a hydraulic head of fluid which provides a bottom hole pressure greater than reservoir pressure, can only be accomplished by squeezing the wellbore contents back into the formation or circulating across the wellhead using the Volumetric Technique. Squeezing large volumes of fluids back into the formation is undesirable in many cases since any rust, scale, or other particulates will be lodged in the perforation or formation matrix. Thus killing such wells will result in a compromise between safety and subsequent productivity. In most squeeze operations, the required injection pressures would increase as fluids are reinjected, which may cause concern over casing burst limitations. For the large diameter casing, the heavier full-weight fluid may under-run the lighter hydrocarbon and inhibit the squeeze process.
For most wells, either the productivity does not merit the use of such large annular diameters or the difficulties in well killing is significant; hence, there is a limitation for such single-zone completion in areas of very high well productivity. However, it can be a reasonably reliable completion with long life and minimal major workover requirements given its fundamental design, provided that it does not suffer from abrasion or corrosion of the production casing types.
A variant of this approach is sometimes applied to multiple zones whereby once the borehole is drilled down through all the zones, individual tubing strings are located in the opposite zone, the entire borehole cemented and each tubing string perforated with orientated guns. This approach is the simplest method of completing a multi-zone borehole, but the drastic nature of its design precludes workovers if problems subsequently arise. This type of completion is known as “tubingless completion.”
Casing and Tubing Flow For Single Zone Completion.
We usually install production tubing and allow flow up the tubing and the tubing-casing annulus. This completion technique has the significant advantage of providing a circulation capability deep in the well where reservoir fluids can be displaced to the surface by an injected kill fluid of the required density to provide hydraulic overbalance on the reservoir. This capability to U-tube fluid between the annulus and the tubing removes the necessity for reinjection into the reservoir. It would not require the high pressures associated with squeeze operations. Provided no erosive or corrosive compounds exist in the flow stream, this completion benefits high-flow rate wells.
Tubing Flow Without Annular Isolation.
In situations where annular flow in a casing-string completion would result in high flowing pressure loss and potential instability, consideration could be given to merely closing the annulus at the surface and preventing flow. However, in reservoirs where the flowing BHP is at or below the bubble point, gas, as it flows from the formation, will migrate upwards under buoyancy forces, and some gas will accumulate in the annulus. This will increase the CHP at the surface. Until gas fills it, gas buildup will offload as a gas slug into the tubing base and be produced. This production instability will be cyclical, referred to as the annulus heading.
In this type of completion, the casing is exposed continuously to produced fluid with the possibility of erosion or corrosion. This, coupled with the potential for annular heading, suggests that unless annular flow is required, the annulus should not be left open to production, despite its simple design.
Tubing Flow With Annular Isolation (The Common Single Zone Completion).
In most cases where tubing flow will occur, the annulus is usually isolated by the installation of a packer. The packer is typically located as close to the top of the reservoir as possible to minimize the trapped annular volume beneath the packer and hence the volume of gas which could accumulate there. However, if the packer is installed, the ability to U-tube or circulate fluid between the tubing and annulus is removed. If such a circulation capability is required, installing a tubing component that will allow annulus communication is necessary. In both cases, the circulation point usually is as deep in the well as possible but above the packer.
This completion system is by far the most widely used and offers maximum well security and control.