Submersible Rigs are a mobile drilling units that have a bottom support. This idea came from making a barge sit on the bottom of Louisiana swamps with drilling platforms welded on top. Thus came the first submersible, a totally submerged, conventional-sized barge. It also has columns high enough to support a platform at a safe above-water distance. Pontoons on either side of the barge provided both stability and displacement control.
Principle Of Work
Generally, we use submersible drilling rigs in shallow waters such as rivers and bays. We can say in waters up to 50 ft deep. One submersible, however, has been used in 175-ft water depths. The submersible has two hulls. Sometimes, we call the upper hull ‘Texas’ deck. Its primary function is to house the rig personnel quarters and equipment. In addition, the performance of the drilling process will be through a slot on the stern with a cantilevered structure. The lower hull is the ballast area. In addition, we use it as a foundation while drilling.
After floating the submersible to a location like a conventional barge, we make it ballasted to rest on the river bottom. The design of the lower hulls allows it to withstand the weight of the total unit and the drilling load. Stability while ballasting these units is a critical factor, although attaching pontoons at each long end solved this problem. Initially, ballast one pontoon until that end of the unit sat on the bottom. Then, after ensuring stability, ballast the other pontoon until the unit rested on the bottom with topside-up every time. Today, however, submersibles are fading from the scene simply because current water depth requirements have surpassed their capabilities. Their water-depth restriction is because of the free-standing height of the units while towing from one place to the other.
Types Of Submersible Drilling Rigs
Since the drilling rig needs to be able to move away from the wellhead after drilling the well, submersibles tend to be of a triangular or rectangular design with a rig derrick at one end of the rig. A design with a centrally located derrick, like most semi-submersibles, cannot move away from a free-standing wellhead without using a sea bed or mud line type of completion. We can group submersibles into two main types:
- Barge Shaped
- Column Design
Barge Shaped
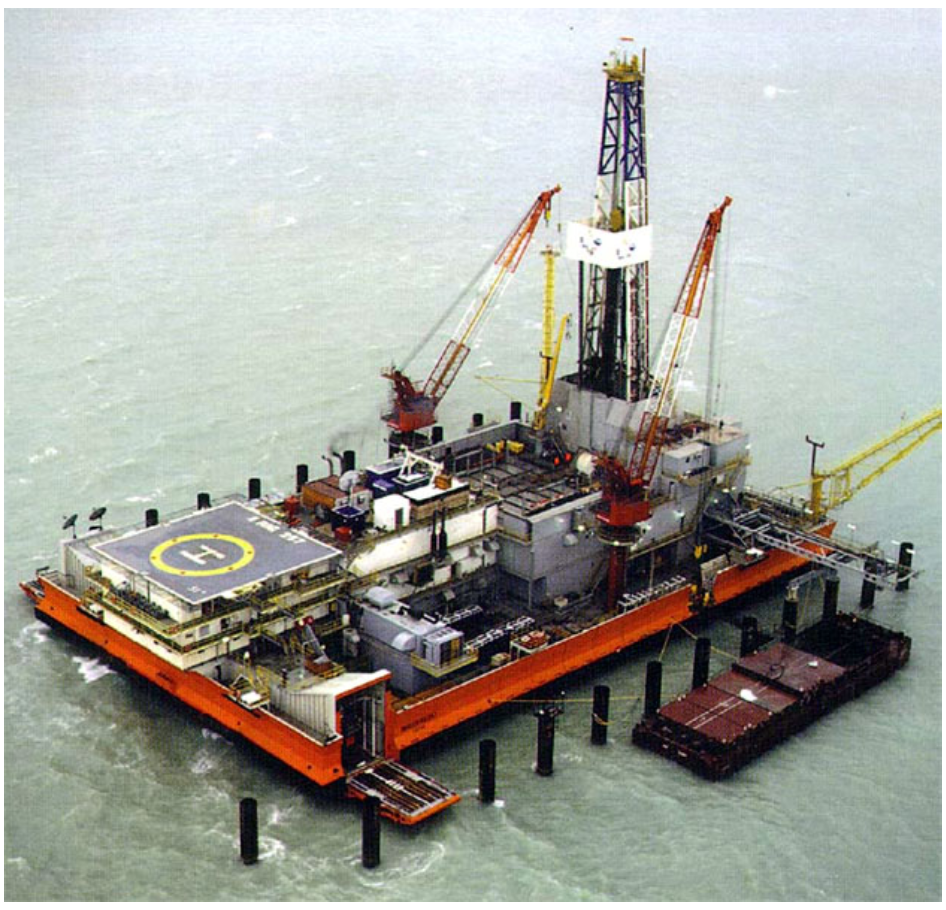
Their main application is in shallow water depths of up to 6 m. Typically the barge size will be 60 m x 18 m with a drilling capability of 6,000 – 7,000 m. Many know this rig as a swamp barge. Its primary utilization is in swamp areas where it is customary to dredge a channel or drilling slot before bringing the rig into a location. The barge has a flat bottom requiring a flat dredged surface on which to sit. To avoid scouring, we always use the barge in ‘still’ water or drilling slots, never in rivers. Most swamp barges have a leveling device on the derrick and substructure to cope with a slight bottom gradient or subsidence during the drilling operation. Some barges have posts extending between the barge and main deck, giving the unit a more significant water depth capability.
The barge-type base unit undergoes a critical period during the raising and sinking operations. During such operations, the basic principle is always to maintain positive stability. We can achieve this by ensuring support for one end of the barge in the floating condition with adequate freeboard. Or, it is resting on the bottom with sufficient negative buoyancy. We can accomplish this by either pumping out or flooding only one end of the barge at a time. Fixed hull extensions give the hull a wider beam and improve stability.
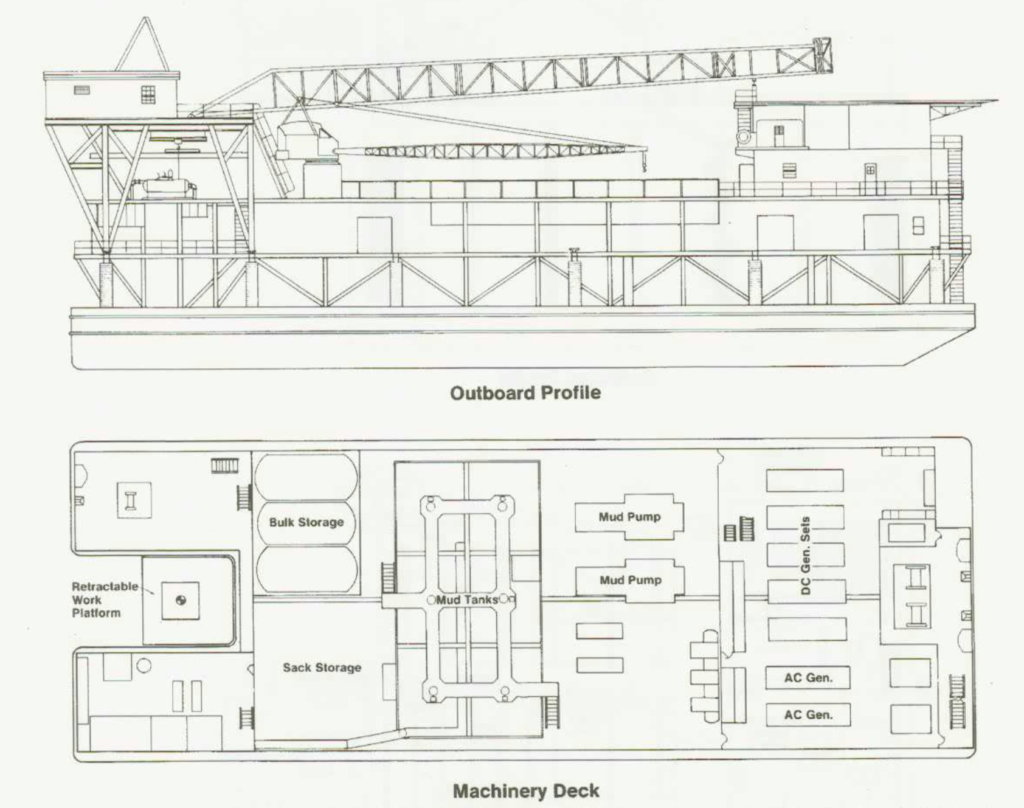
We typically find Barge-shaped submersible rigs in the Gulf of Mexico, Nigeria, and East Kalimantan. They are not particularly common, and only approximately twelve are operating worldwide. Figure 1 shows an example of a typically posted swamp barge operating in Nigeria.
Submersible Drilling Rig – Column Design
The column design submersible gives a more significant water depth capability, typically up to 25 m. Most offshore drilling rig types have a triangular or square deck shape, typically 60 m x 50 m. The derrick, as we mentioned previously, will normally overhang one end. Or, we mount the derrick over a slot to allow the rig to move off and leave a free-standing wellhead.
Some early semi-submersible rigs could sit on the bottom in water depths of up to 35 meters and operate in floating mode. Still, this type has fallen from favor as semi-submersibles generally became larger. The design of most modern semi-submersibles no longer allows sitting on the bottom, though most could be modified to do so by moving seawater intakes. This, however, is not an economic proposition since there is an abundance of shallow water jackup rigs available.
Oil and gas Companies can load the rigs heavily with supplies when sitting on the bottom. However, the allowable deck load will only be 500-700 tonnes during rig moves. This submersible type is also sensitive to sea bed gradients, so the location must be pretty level.
The column-type base units have a vast beam and are equipped with large-diameter vertical columns at the corners of the base. This setup gives sufficient stability so that raising or sinking will be achievable evenly.
We can typically find column-design submersible rigs in the Gulf of Mexico. In 1995, all 12 rigs of this type listed by World Oil’s Marine Drilling Rig ’95 Summary were operating in the Gulf. Their numbers, though, are in decline. Figure 2 shows an example of a typical column-design submersible offshore drilling rig.
Moving Barge Rigs
Before any marine movement operations commence, it is imperative to review local regulations for notices. The target of this review is to ensure the required permission. We can use this information to evaluate the potential impacts of drilling operations. Furthermore, we can identify mitigating options. It is necessary to post valid discharge and drilling permits from authorized agencies at the rig before spud.
The following general operational guidelines apply to the barge during the preparation and execution of transit operations.
- Document the marine procedure following the drilling contractor’s Marine Operation Manual.
- If historical data is absent, analyze a soil bore sample to facilitate the design/building of a rockpad.
- Surveying and dredging arrangements will be made well in advance.
- Towing arrangements will be made well in advance.
- Size and number of tow vessels required considering:
- Government regulations
- Contractor’s insurance requirement
- Expected weather
- Distance of tow
- Positioning requirements at the mobilization location and final drilling site.
- Secure all equipment on board adequately before the rig moves. Particular attention will be given to the BOP stack and tubular goods.
- Description and/or map of tow route and location of pipeline crossings and other facilities that could impact rig move.
- A contingency procedure will be in place for heavy weather, including:
- Pre-determined safe shelter locations or locations along the route.
- For barge rig moves, the payment details should be specified in the drilling contract (i.e., day rate or lump sum).
Submersible Drilling Rig Conclusion:
- Swamp submersible drilling barge rigs were explicitly built to drill in shallow water, swamps or delta rivers, where a jack-up or semisub cannot operate.
- They are designed to operate in 10 – 15 ft of water.
- Swamp barges are towed in position with Supply Vessels. Once on, they take on sea water to sit on the sea bed.
- Sunkar (Parker Drilling Co.) is a swamp barge modified to work in the Caspian Sea.
- Swamp barges are usually employed in Nigeria (Niger River Delta), Venezuela, and the
Caspian Sea. - Posted barges are designed for depths up to 100 ft, a much deeper range than a swamp barge.