The traveling block (one of the rig components) is a diamond-shaped block containing several sheaves, always less than those in the crown block. The drilling line is wound continuously on the crown and traveling blocks, with the two outer ends, wound on the hoisting drum and attached to the deadline anchor.
Traveling block specs are much similar to crown block. The diameter and groove of the pulleys will depend on the drilling line dimensions we plan to use. The manufacturer determines these values as per API RP 9B. Same as the crown block, the proportion of the sheave diameter to the drilling line should be between 30-40:1. The traveling blocks are built as per API Spec. 8A and 8C.
Function Of Rig Traveling Block
This block is a set of sheaves (pulleys) that move up and down in the derrick. The drilling line is threaded (reeved) over the sheaves on the crown and through the sheaves in the traveling block. This provides a significant mechanical advantage to the drill line, enabling it to lift heavy loads of pipe and casing. The number of pulleys used on the traveling Block will be from five to eight, providing a variable capacity to the Hoisting system.
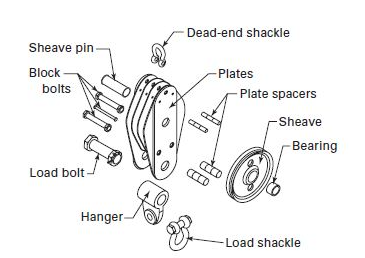
Types & Characteristics
The size of the groove should be the same as the diameter of the drilling line to deliver the proper support. A tiny pulley groove could cause high friction. Furthermore, it can cause erosion in the line. In addition, an oversized one can flatten the drilling line.
Standard Type
- Standard Rig Traveling Block
- Dimensional characteristics
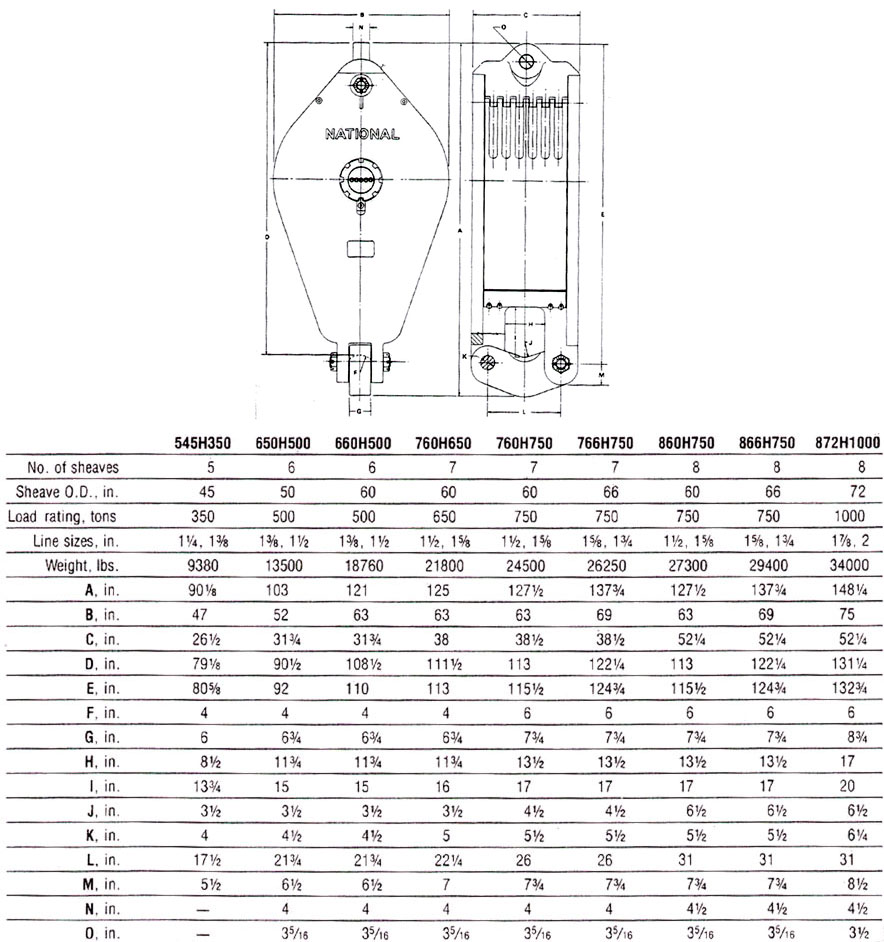
Unitized type
- Scheme and Nomenclature
- Unitized Type
Combination With a Hook type
- Scheme and Nomenclature
- Combination Traveling Block
Maritime Traveling Block Type
Traveling Block Inspection
Periodic inspections: The Rig Traveling Block, as with all Hoisting equipment, must be inspected according to the manufacturer’s recommendations and API RP 8B or related ISO (International Organization for Standardization) 13534. A standard policy requires Category IV inspection (as per API RP 8B and ISO 13534) every five years.
The frequency of periodic inspections is as follows:
- Five-year
- Annual
- Semi-annual
- Monthly
- Daily
API Recommended Practice 8B Categories:
- Category I: Observe the equipment during its operation for any unsatisfactory performance.
- Category II: This one will include the previous category. In addition to that, we should perform proper lubrication, corrosion inspection, deformation, visible external cracks, loose or missing components, deterioration, and adjustment.
- Category III: This one will include the previous category, plus further NDE inspection, and may include wear inspection for the internal parts to figure if it exceeds the standard tolerances set bu the manufacturer. All these category items shall be done on a semi-annual basis.
- Category IV: This category includes the previous inspection, plus full NDE inspection of all primary load-carrying components as defined by the manufacturer. Some of these inspections shall be on annual basis, and some every 5 years.